What Worked in Cost Reduction During the 2020s: A Decade of Financial Efficiency
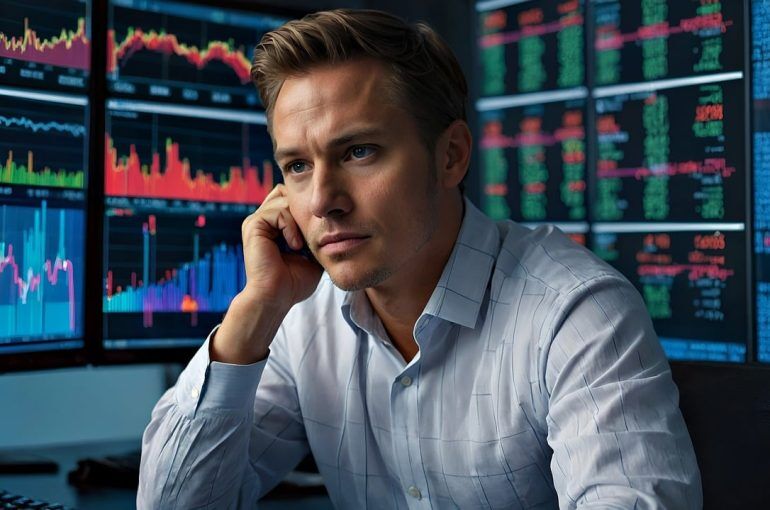
What Worked in Cost Reduction During the 2020s: A Decade of Financial Efficiency
The Need for Cost Reduction in the 2020s
Economic Uncertainty and Global Challenges
The 2020s have been marked by significant economic uncertainty and global challenges that have necessitated a focus on cost reduction. The decade began with the COVID-19 pandemic, which disrupted global supply chains, altered consumer behavior, and led to widespread economic instability. Businesses faced unprecedented challenges in maintaining operations while managing reduced revenues and increased costs. This environment underscored the importance of financial efficiency and cost management as essential strategies for survival and growth.
Technological Advancements and Digital Transformation
The rapid pace of technological advancements and digital transformation has also driven the need for cost reduction. Companies have been compelled to invest in new technologies to remain competitive, which often requires reallocating resources and optimizing existing processes. The integration of automation, artificial intelligence, and data analytics has enabled businesses to streamline operations, reduce waste, and enhance productivity. These technological shifts have highlighted the necessity of cost reduction strategies to fund innovation and maintain a competitive edge.
Environmental and Sustainability Pressures
Environmental concerns and sustainability pressures have further emphasized the need for cost reduction. As businesses strive to meet regulatory requirements and consumer expectations for sustainable practices, they must find ways to reduce costs associated with energy consumption, waste management, and resource utilization. Implementing sustainable practices often involves upfront investments, making cost reduction a critical component of achieving long-term environmental goals without compromising financial performance.
Competitive Market Dynamics
The competitive landscape of the 2020s has intensified, with businesses facing increased pressure to deliver value to customers while maintaining profitability. Globalization and the rise of digital platforms have lowered barriers to entry, leading to heightened competition across industries. To remain competitive, companies must focus on cost reduction to offer competitive pricing, improve margins, and invest in customer experience enhancements. This competitive pressure has made cost efficiency a strategic imperative for businesses seeking to differentiate themselves in the market.
Workforce and Labor Market Shifts
Shifts in the workforce and labor market have also contributed to the need for cost reduction. The rise of remote work, gig economy, and changing employee expectations have transformed traditional employment models. Companies are reevaluating their workforce strategies to optimize labor costs while attracting and retaining talent. This includes leveraging flexible work arrangements, outsourcing, and investing in employee development to enhance productivity and reduce turnover costs. These labor market dynamics have reinforced the importance of cost reduction in managing human capital effectively.
Technological Innovations and Automation
The Rise of Artificial Intelligence and Machine Learning
Artificial Intelligence (AI) and Machine Learning (ML) have been at the forefront of technological innovations in the 2020s, driving significant cost reductions across various industries. AI and ML algorithms have enabled businesses to automate complex processes, leading to increased efficiency and reduced labor costs. These technologies have been particularly effective in areas such as predictive maintenance, where they help anticipate equipment failures and reduce downtime, and in customer service, where AI-driven chatbots handle routine inquiries, freeing up human resources for more complex tasks.
Robotics and Process Automation
Robotic Process Automation (RPA) has transformed the way businesses handle repetitive tasks. By deploying software robots to perform routine operations, companies have been able to streamline workflows and reduce the need for manual intervention. This has not only cut down on labor costs but also minimized errors, leading to improved accuracy and efficiency. In manufacturing, the use of robotics has optimized production lines, allowing for faster and more precise operations, which in turn has reduced waste and operational costs.
Cloud Computing and Infrastructure Optimization
The shift to cloud computing has been a game-changer for cost reduction in the 2020s. By migrating to cloud-based solutions, companies have been able to eliminate the need for expensive on-premises infrastructure, leading to significant savings on hardware and maintenance costs. Cloud computing also offers scalable resources, allowing businesses to pay only for what they use, which optimizes operational expenses. Furthermore, cloud platforms have facilitated remote work, reducing the need for physical office space and associated costs. Reach out to Exec Capital Today.
Internet of Things (IoT) and Smart Technologies
The integration of Internet of Things (IoT) devices has enabled businesses to gather real-time data and optimize operations. IoT technology has been instrumental in reducing costs through enhanced monitoring and control of resources. For example, smart energy management systems have allowed companies to track and reduce energy consumption, leading to lower utility bills. In logistics, IoT sensors have improved supply chain efficiency by providing real-time tracking and inventory management, reducing waste and ensuring timely deliveries.
Data Analytics and Business Intelligence
Data analytics and business intelligence tools have empowered organizations to make data-driven decisions, leading to cost reductions. By analyzing large volumes of data, companies can identify inefficiencies and areas for improvement. Predictive analytics has been particularly useful in forecasting demand and optimizing inventory levels, reducing excess stock and associated holding costs. Business intelligence platforms have also facilitated better financial planning and budgeting, enabling organizations to allocate resources more effectively.
Cybersecurity Innovations
As businesses have increasingly relied on digital solutions, cybersecurity has become a critical area of focus. Innovations in cybersecurity have helped protect organizations from costly data breaches and cyberattacks. Advanced threat detection systems and automated security protocols have reduced the need for extensive manual monitoring, lowering operational costs. By safeguarding sensitive information, companies have avoided the financial and reputational damage associated with security incidents, contributing to overall cost efficiency.
Remote Work and Its Impact on Operational Costs
Reduction in Office Space Requirements
The shift to remote work has significantly reduced the need for large office spaces. Companies have been able to downsize their physical footprints, leading to substantial savings on rent, utilities, and maintenance. Many organizations have adopted flexible workspace solutions, such as hot-desking or shared office spaces, further optimizing their real estate expenses.
Decrease in Overhead Costs
Remote work has led to a decrease in various overhead costs associated with maintaining a physical office. Expenses related to office supplies, furniture, and equipment have been minimized. The need for on-site amenities, such as cafeterias and parking facilities, has also diminished, contributing to cost savings.
Lowered Utility Expenses
With fewer employees working on-site, companies have experienced a reduction in utility expenses, including electricity, water, and heating/cooling costs. This decrease in energy consumption not only reduces operational costs but also supports sustainability initiatives by lowering the organization’s carbon footprint.
Impact on Employee-Related Costs
Remote work has influenced employee-related costs in several ways. Companies have been able to reduce expenses related to commuting subsidies, travel allowances, and relocation packages. Moreover, remote work has enabled organizations to tap into a global talent pool, potentially lowering salary expenses by hiring in regions with lower cost-of-living standards.
Technology and Infrastructure Investments
While remote work has led to cost reductions in several areas, it has also necessitated investments in technology and infrastructure. Companies have had to allocate resources for secure and reliable communication tools, cloud services, and cybersecurity measures. These investments, however, are often offset by the savings achieved in other operational areas.
Impact on Productivity and Efficiency
Remote work has had a mixed impact on productivity and efficiency, which indirectly affects operational costs. Some organizations have reported increased productivity due to flexible work arrangements and reduced commute times. However, others have faced challenges related to collaboration and communication, necessitating investments in team-building and management strategies to maintain efficiency.
Long-Term Strategic Planning
The adoption of remote work has prompted companies to rethink their long-term strategic planning. Organizations are increasingly considering hybrid work models, which combine remote and in-office work, to optimize operational costs while maintaining employee satisfaction and productivity. This shift requires careful planning and analysis to balance cost savings with potential challenges in workforce management.
Supply Chain Optimization and Management
Technological Advancements
Automation and Robotics
The 2020s saw a significant increase in the adoption of automation and robotics within supply chains. Companies leveraged these technologies to streamline operations, reduce human error, and increase efficiency. Automated systems in warehouses, such as robotic picking and packing, improved speed and accuracy, leading to cost savings and enhanced productivity.
Internet of Things (IoT)
IoT devices became integral in supply chain management, providing real-time data and insights. Sensors and connected devices allowed for better tracking of goods, monitoring of environmental conditions, and predictive maintenance of equipment. This connectivity enabled companies to optimize routes, reduce delays, and minimize waste, ultimately lowering costs.
Artificial Intelligence and Machine Learning
AI and machine learning algorithms were employed to analyze vast amounts of data, enabling more accurate demand forecasting and inventory management. These technologies helped companies anticipate market changes, adjust production schedules, and optimize stock levels, reducing excess inventory and associated costs.
Strategic Sourcing and Supplier Relationships
Supplier Diversification
To mitigate risks and reduce costs, companies diversified their supplier base. By sourcing materials and components from multiple suppliers, businesses reduced dependency on single sources, improved negotiation power, and ensured more competitive pricing.
Long-term Partnerships
Building long-term relationships with key suppliers became a strategic focus. These partnerships fostered collaboration, innovation, and trust, leading to better terms, shared risks, and joint cost-reduction initiatives. Companies that invested in these relationships often benefited from improved service levels and reduced procurement costs.
Lean and Agile Practices
Just-in-Time (JIT) Inventory
The adoption of JIT inventory practices helped companies minimize holding costs and reduce waste. By aligning production schedules closely with demand, businesses maintained lower inventory levels, freeing up capital and reducing storage expenses.
Agile Supply Chain Models
Agility in supply chain management allowed companies to respond quickly to market changes and disruptions. Flexible production processes, adaptable logistics, and rapid decision-making capabilities enabled businesses to maintain service levels while controlling costs.
Sustainability and Green Initiatives
Eco-friendly Packaging
Companies increasingly adopted sustainable packaging solutions to reduce environmental impact and costs. By using recyclable materials and optimizing packaging sizes, businesses not only met consumer demand for eco-friendly products but also reduced material and shipping expenses.
Energy Efficiency
Investments in energy-efficient technologies and practices helped companies lower operational costs. From optimizing transportation routes to implementing energy-saving measures in production facilities, businesses reduced their carbon footprint and achieved significant cost savings.
Data-Driven Decision Making
Advanced Analytics
The use of advanced analytics tools provided companies with deeper insights into their supply chain operations. By analyzing data on supplier performance, logistics, and market trends, businesses made informed decisions that optimized processes and reduced costs.
Real-time Monitoring
Real-time monitoring of supply chain activities enabled companies to identify and address issues promptly. This proactive approach minimized disruptions, improved service levels, and reduced the costs associated with delays and inefficiencies.
Energy Efficiency and Sustainable Practices
Technological Innovations
Smart Grids and Meters
Smart grids and meters have revolutionized energy management by providing real-time data and analytics. These technologies enable businesses to monitor and optimize their energy consumption, leading to significant cost savings. By identifying peak usage times and adjusting energy use accordingly, companies can reduce their energy bills and improve overall efficiency.
LED Lighting
The widespread adoption of LED lighting has been a game-changer in reducing energy costs. LEDs consume significantly less power than traditional incandescent bulbs and have a longer lifespan, which reduces maintenance costs. The initial investment in LED technology is quickly offset by the savings in energy consumption and replacement costs.
Energy Management Systems
Energy management systems (EMS) integrate various technologies to monitor, control, and optimize energy use in buildings and industrial processes. These systems provide insights into energy consumption patterns and help identify areas for improvement. By automating energy-saving measures, EMS can lead to substantial cost reductions.
Renewable Energy Sources
Solar Power
The decreasing cost of solar panels and advancements in photovoltaic technology have made solar power a viable option for many businesses. Installing solar panels can significantly reduce reliance on grid electricity, leading to lower energy bills. In some cases, companies can even sell excess energy back to the grid, creating an additional revenue stream.
Wind Energy
Wind energy has become an increasingly popular renewable energy source due to its scalability and declining costs. Businesses located in areas with consistent wind patterns can benefit from installing wind turbines, which can provide a substantial portion of their energy needs. This reduces dependency on fossil fuels and stabilizes energy costs.
Sustainable Practices
Green Building Design
Incorporating sustainable design principles in new construction and retrofitting existing buildings can lead to significant energy savings. Features such as improved insulation, energy-efficient windows, and passive solar design reduce the need for heating and cooling, lowering energy costs. Green buildings also often qualify for tax incentives and rebates, further enhancing cost savings.
Waste Reduction and Recycling
Implementing waste reduction and recycling programs can lead to cost savings by minimizing waste disposal fees and reducing the need for raw materials. By reusing materials and recycling waste, companies can lower their environmental impact and improve their bottom line. These practices also enhance brand reputation and customer loyalty.
Water Conservation
Water conservation measures, such as installing low-flow fixtures and using recycled water for non-potable applications, can significantly reduce water bills. Efficient water management not only cuts costs but also ensures compliance with regulations and reduces the environmental footprint of a business.
Strategic Outsourcing and Partnerships
Evolution of Outsourcing in the 2020s
The 2020s witnessed a significant evolution in outsourcing strategies, driven by technological advancements and the need for businesses to remain competitive in a rapidly changing global market. Companies increasingly turned to outsourcing not just for cost reduction, but also to access specialized skills and technologies that were not available in-house. This shift was facilitated by the rise of digital platforms and communication tools that made remote collaboration more efficient and effective.
Benefits of Strategic Outsourcing
Cost Efficiency
Strategic outsourcing allowed companies to reduce operational costs by leveraging the expertise and economies of scale offered by specialized service providers. By outsourcing non-core functions, businesses could focus their resources on areas that directly contributed to their competitive advantage. This approach enabled firms to convert fixed costs into variable costs, providing greater financial flexibility.
Access to Expertise and Innovation
Outsourcing provided access to a global talent pool, enabling companies to tap into specialized skills and innovative solutions that were not readily available internally. This access to external expertise allowed businesses to accelerate their innovation cycles and bring new products and services to market more quickly.
Scalability and Flexibility
Outsourcing offered companies the ability to scale operations up or down in response to market demands without the need for significant capital investment. This flexibility was particularly valuable in industries with fluctuating demand, allowing businesses to maintain efficiency and responsiveness.
Strategic Partnerships
Collaborative Innovation
Strategic partnerships went beyond traditional outsourcing by fostering collaborative innovation. Companies formed alliances with other firms, including competitors, to co-develop new technologies and solutions. These partnerships enabled shared risk and investment, leading to breakthroughs that would have been difficult to achieve independently.
Enhanced Market Reach
Partnerships allowed companies to expand their market reach by leveraging the distribution networks and customer bases of their partners. This approach was particularly effective in entering new geographic markets or segments, where local knowledge and established relationships were crucial for success.
Shared Resources and Capabilities
Through strategic partnerships, companies could share resources and capabilities, reducing duplication of efforts and maximizing efficiency. This collaboration often involved joint ventures or co-branding initiatives, where partners pooled their strengths to achieve common goals.
Challenges and Considerations
Managing Outsourced Relationships
Effective management of outsourced relationships was critical to realizing the benefits of outsourcing. Companies needed to establish clear communication channels, performance metrics, and governance structures to ensure alignment with their strategic objectives. Trust and transparency were essential components of successful outsourcing arrangements.
Balancing Control and Flexibility
While outsourcing and partnerships offered flexibility, they also required companies to relinquish some control over certain functions. Striking the right balance between control and flexibility was crucial to maintaining quality and consistency in outsourced operations.
Cultural and Operational Alignment
Cultural and operational alignment between partners was vital for the success of strategic partnerships. Differences in corporate culture, business practices, and regulatory environments could pose challenges, requiring careful negotiation and alignment of objectives and expectations.
Lean Management and Process Improvement
Understanding Lean Management
Lean management is a systematic approach to identifying and eliminating waste through continuous improvement, focusing on delivering value to the customer. Originating from the Toyota Production System, lean management has been widely adopted across various industries due to its effectiveness in enhancing operational efficiency and reducing costs. The core principles of lean management include defining value from the customer’s perspective, mapping the value stream, creating flow, establishing pull, and pursuing perfection.
Key Principles of Lean Management
Defining Value
Value is defined by the customer and is based on their needs and expectations. In lean management, organizations strive to understand what the customer values and focus their efforts on delivering that value efficiently. This involves identifying and eliminating activities that do not add value to the customer, thereby reducing costs and improving service delivery.
Mapping the Value Stream
Mapping the value stream involves analyzing the flow of materials and information required to bring a product or service to the customer. By visualizing the entire process, organizations can identify areas of waste, such as excess inventory, waiting times, and unnecessary movements. This enables them to streamline operations and reduce costs by eliminating non-value-adding activities.
Creating Flow
Creating flow ensures that the production process moves smoothly without interruptions or delays. This involves organizing workstations, balancing workloads, and optimizing the layout of facilities to minimize bottlenecks and improve efficiency. By creating a seamless flow, organizations can reduce lead times, lower inventory levels, and enhance overall productivity.
Establishing Pull
The pull system is a key component of lean management, where production is based on actual customer demand rather than forecasts. This approach helps organizations avoid overproduction and excess inventory, leading to significant cost savings. By aligning production with customer demand, companies can respond more quickly to market changes and reduce waste.
Pursuing Perfection
Continuous improvement is at the heart of lean management. Organizations are encouraged to constantly seek ways to improve processes, eliminate waste, and enhance value delivery. This involves fostering a culture of innovation and employee involvement, where everyone is empowered to identify and implement improvements. By pursuing perfection, companies can achieve long-term cost reductions and maintain a competitive edge.
Process Improvement Techniques
Kaizen
Kaizen, meaning “change for better” in Japanese, is a philosophy that focuses on continuous, incremental improvements in processes. It involves engaging employees at all levels to identify inefficiencies and suggest improvements. Kaizen events or workshops are often conducted to address specific issues, leading to immediate and tangible cost savings.
Six Sigma
Six Sigma is a data-driven methodology aimed at reducing defects and improving quality in processes. By using statistical tools and techniques, organizations can identify root causes of variability and implement solutions to enhance process performance. Six Sigma projects often result in significant cost reductions by minimizing errors, rework, and waste.
Value Stream Mapping
Value stream mapping is a visual tool used to analyze and design the flow of materials and information in a process. By mapping the current state and envisioning a future state, organizations can identify areas for improvement and develop action plans to achieve cost savings. This technique helps in pinpointing bottlenecks, redundancies, and inefficiencies that contribute to higher costs.
Just-In-Time (JIT)
Just-In-Time is a production strategy that aims to reduce inventory levels and associated carrying costs by producing goods only as they are needed. By synchronizing production with demand, organizations can minimize waste, reduce storage costs, and improve cash flow. JIT requires close collaboration with suppliers and a responsive supply chain to be effective.
Benefits of Lean Management and Process Improvement
Implementing lean management and process improvement techniques can lead to substantial cost reductions and operational efficiencies. Organizations can achieve lower production costs, reduced lead times, and improved product quality. Moreover, by fostering a culture of continuous improvement, companies can enhance employee engagement and drive innovation. These benefits contribute to a more agile and competitive organization, capable of adapting to changing market conditions and customer demands.
Lessons Learned
Embracing Technology and Automation
The 2020s demonstrated the critical role of technology and automation in cost reduction. Companies that invested in digital transformation, AI, and machine learning were able to streamline operations, reduce labor costs, and enhance productivity. Automation of routine tasks allowed businesses to allocate human resources to more strategic roles, driving innovation and efficiency.
Importance of Data-Driven Decision Making
Data analytics emerged as a cornerstone for financial efficiency. Organizations that harnessed big data and analytics tools were better equipped to identify cost-saving opportunities, optimize supply chains, and forecast financial trends. This data-driven approach enabled more informed decision-making, reducing waste and improving resource allocation.
Agile and Flexible Business Models
The decade highlighted the necessity for agility in business operations. Companies that adopted flexible business models were able to quickly adapt to market changes, economic disruptions, and consumer demands. This adaptability not only reduced costs associated with rigid structures but also allowed businesses to capitalize on new opportunities swiftly.
Sustainable Practices as Cost-Saving Measures
Sustainability initiatives proved to be more than just ethical choices; they became effective cost-reduction strategies. By implementing energy-efficient practices, reducing waste, and optimizing resource use, companies not only lowered operational costs but also enhanced their brand reputation and customer loyalty.
Remote Work and Workforce Optimization
The shift to remote work during the 2020s offered significant cost savings in terms of reduced office space requirements and associated overheads. Companies that embraced flexible work arrangements found that they could maintain productivity while reducing expenses. This shift also led to a reevaluation of workforce needs, promoting a more efficient allocation of human resources.
Future Implications
Continued Investment in Technology
As technology continues to evolve, ongoing investment in digital tools and platforms will be crucial for maintaining cost efficiency. Future advancements in AI, machine learning, and blockchain technology are expected to offer new avenues for reducing costs and enhancing operational efficiency.
Focus on Resilience and Risk Management
The experiences of the 2020s underscored the importance of building resilient business models. Future strategies will likely emphasize risk management and contingency planning to mitigate the impact of unforeseen disruptions, ensuring financial stability and cost control.
Evolving Workforce Dynamics
The future will see further evolution in workforce dynamics, with a continued emphasis on remote work and flexible employment models. Companies will need to balance cost savings with employee engagement and productivity, leveraging technology to support a distributed workforce.
Integration of Sustainability into Core Strategies
Sustainability will become increasingly integrated into core business strategies, not only as a cost-saving measure but as a driver of innovation and competitive advantage. Companies will need to align their financial goals with environmental and social responsibilities to meet stakeholder expectations and regulatory requirements.
Emphasis on Collaborative Ecosystems
The future will likely see a greater emphasis on collaborative ecosystems, where businesses partner with suppliers, customers, and even competitors to achieve cost efficiencies. These ecosystems will enable shared resources, knowledge, and innovations, driving down costs and fostering mutual growth.
Adrian Lawrence FCA with over 25 years of experience as a finance leader and a Chartered Accountant, BSc graduate from Queen Mary College, University of London.
I help my clients achieve their growth and success goals by delivering value and results in areas such as Financial Modelling, Finance Raising, M&A, Due Diligence, cash flow management, and reporting. I am passionate about supporting SMEs and entrepreneurs with reliable and professional Chief Financial Officer or Finance Director services.